High-Visibility Safety Apparel
On this page
- What is High-Visibility Safety Apparel (HVSA)?
- Why do I need High-Visibility Safety Apparel?
- When do I need High-Visibility Safety Apparel?
- Can I add a logo or name tag to the High-Visibility Apparel?
- What is the difference between fluorescent and retroreflective materials?
- What should I look for in High-Visibility Safety Apparel?
- What are the different classes of safety apparel?
- When would I wear the different classes of High-Visibility Safety Apparel?
- What should worker training include?
What is High-Visibility Safety Apparel (HVSA)?
Back to topHigh-visibility safety apparel (HVSA) is clothing (e.g., vests, bibs, or coveralls) that workers can wear to improve how well other people "see" them (their visibility). Most often, high-visibility clothing is worn to alert drivers and other vehicle operators of a worker's presence, especially in low light and dark conditions. High-visibility headwear can also be worn to increase the visibility of the wearer in situations where part or all of the wearer's body could be obscured (e.g., leaves/trees, traffic barriers, construction materials, etc.).
Design requirements for high-visibility safety clothing are generally found in the CSA Standard Z96-15 (R2020), High-Visibility Safety Apperal. In the United States, the design requirements are outlined in the ANSI/ISEA 107-2015 2020 American National Standard for High-visibility Safety Apparel and Accessories.
Why do I need High-Visibility Safety Apparel?
Back to topHigh-visibility safety apparel (HVSA) is needed if you work when there is low light and poor visibility, especially if you are working around moving vehicles (cars, trucks or other machinery traveling under their own power, such as , forklifts, backhoes, etc). High-visibility items allow you to be seen by the drivers of those vehicles from farther away so that they can respond accordingly, which increases your safety at work. The human eye responds best to large, contrasting, bright or moving objects. Worker visibility is enhanced by high colour contrast between clothing and the work environment against which it is seen.
When do I need High-Visibility Safety Apparel?
Back to topBefore selecting any high-visibility safety apparel, always confirm the legislative requirements for your jurisdiction. For example, certain tasks may require specific apparel.
The CSA Standard recommends that a hazard assessment be carried out on each job site to evaluate the workplace or work site for known or potential hazards a worker can encounter while performing a job or task. This assessment helps determine the risk to workers of being hit by moving vehicles and the environmental conditions under which work is performed. For more information about risk assessments, please see the OSH Answers document Risk Assessment.
When doing a hazard assessment where HVSA might be required, be sure to consider:
- The type and nature of the work:
- Do workers and mobile equipment need to interact?
- Are workers controlling traffic or interacting with the public?
- Do workers need to be visually identifiable from others in the area?
- Are there industry specifications or good practices?
- Potential exposures to heat or flames.
- Work conditions, such as indoor or outdoor work, temperature, work rates, traffic flow, traffic volume, visibility, etc.
- The workplace environment and the background workers must be seen in (e.g., is the visual area behind the workers simple, complex, urban, rural, highway, filled with equipment, cluttered).
- How long the worker is exposed to various traffic hazards, including traffic speeds.
- Lighting conditions and how the natural light might be affected by changing weather (e.g., sunlight, overcast sky, fog, rain, or snow).
- Factors that affect warning distances and times, such as the volume of traffic, the size of vehicles, their potential speeds, the ability to stop quickly, and surface conditions.
- Current controls (e.g., engineering controls such as barricades or administrative control such as training).
- Any distractions that could draw workers attention away from hazards.
- The sightlines of mobile equipment and vehicle operators, especially when vehicles are operated in reverse.
Once the hazards are identified, the employer can select appropriate controls. It is important to eliminate or reduce the hazards using engineering (e.g., physical barriers) and administrative controls (e.g., work during daylight hours). High-visibility apparel is considered to be personal protective equipment, and can be used in addition to other controls.
Can I add a logo or name tag to the High-Visibility Apparel?
Back to topIt depends. According to the CSA Standard, a non-retroreflective identification (ID) badge must be smaller than 105 cm2 and if it is on the front of the garment, can only cover 25 cm2 of either or both of the vertical striping. If the ID badge is on the back, it cannot cover any of the striping. If the ID badge is made of retroreflective striping that meets the requirements of the standard, then the badge can be up to 500 cm2 and be placed anywhere, but should not obscure the pattern of the retroreflective striping.
If the CSA Standard is not specifically referenced in the legislation that applies to your jurisdiction, it is recommended that you contact the government department responsible for occupational health and safety to confirm that alterations are acceptable.
What is the difference between fluorescent and retroreflective materials?
Back to topFluorescent material takes a portion of invisible ultraviolet light from sunlight, and through special pigments, sends it back to the viewer as more visible light. This material only functions where there is a source of natural sunlight. Fluorescent material will appear brighter than the same coloured non-fluorescent material, especially under low natural light (e.g., cloud cover, fog, dusk, dawn, etc.). This property offers daytime visibility enhancement that is not present with other colours. These materials enhance daytime visibility, especially at dawn and dusk. Fluorescent colours provide the greatest contrast against most backgrounds.
Retroreflective material is created to return light in the direction of the light's source. This property will let a driver or equipment operator see the light being reflected from the retroreflective material on a person's garment (as long as the person is standing in the light's beam). Retroreflective materials are most effective under low-light level conditions. While retroreflective materials can still reflect in the daylight, there is little difference between the light reflected from the garment's material and the surrounding environment. This lack of contrast makes retroreflective materials ineffective for enhanced visibility during (sunny) daytime conditions. There are two levels of retroreflective material.
In contrast, reflective materials bounce light off its surface. While the term "reflective" is not used in the CSA standard, it is typically defined as a material or object that has the ability to "throw back" light. Most surfaces are already light reflective.
Combined-performance retroreflective material is a retroreflective material that is also a fluorescent material. Not all retroreflective materials are fluorescent, nor all all fluorescent materials are retroreflective.
What should I look for in High-Visibility Safety Apparel?
Back to topCoverage/Visibility:
- Bright garments are more visible than dull ones. Coverage all around the body (360° full body coverage) provides better visibility in all viewing directions.
- Stripes of colours that contrast (have a distinct colour difference) with the background material can provide increased visibility. Stripes on the arms and legs can also provide visual clues about the motion of the person wearing the garment.
- When background material is bright-coloured or fluorescent material, it can increase visibility, but it does not provide retroreflective properties.
- Other requirements such as flame resistance, thermal performance, water resistance, durability, comfort, tear-away features, material breathability, and flexibility may be required bases on other hazards present.
Employers should select the colour and stripe combination that provides the preferred contrast, visual indication of movement, and direction of travel.
Fit:
- For safety and best performance, garments should fit the person. Proper fit includes wearing the garments as intended and considering any additional clothing worn underneath the high-visibility apparel. The garments should sit correctly on the body and stay in place during work.
- The apparel should be comfortable to wear. Any seams and materials should not cause discomfort or irritation to the wearer (e.g., no sharp edges or projections, no rough material). The apparel should also be of appropriate weight, and provide adequate stretch and flexibility.
- Garments should be selected and worn so that no other clothing or equipment covers the high-visibility materials (e.g., backpacks, glove gauntlets, equipment belts, and high-cut boots).
Brightness:
- Daylight - Bright colours are more visible than dull colours under daylight conditions (e.g. fluorescent materials are suitable for daylight).
- Low light conditions - Fluorescent colours are more effective than bright colours under low light (e.g. dawn and dusk). Under these conditions, reflective materials are also suggested.
- Dark conditions - Retroreflective material provides greater visibility and are preferred over bright colours alone under low light conditions. As fluorescent materials require natural light, they are ineffective at night or when no natural light is present.
Design:
To comply with the CSA Standard, any high-visibility safety apparel must meet the following criteria for the stripes/bands:
- A minimum width of 50 mm.
- A waist-level horizontal stripe/band that goes completely around the body at the navel or belly button.
- Two vertical stripes on the front passing over the shoulders and down to the waist.
- A symmetric "X" on the back extending from the shoulders to the waist.
- For Class 3 apparel, stripes/bands encircling both arms and both legs are added.
Colour:
For all classes, the CSA Z96-15 (R2020), High-Visibility Safety Apparel Standard specifies both the colour of the background and the stripes/bands. For example, class 1 apparel (e.g., harness style) must have a minimum of 0.14 metres squared of background material, while for class 2 and class 3 apparel, full coverage of background material is required. Background material can be fluorescent yellow-green, fluorescent orange-red, fluorescent red bright yellow-green, or bright orange-red.
Care/Maintenance:
- Keep high-visibility apparel clean and well-maintained. Contaminated or dirty retroreflective materials provide lower visibility.
- Replace garments that show signs of wear and tear, soiling, or contamination as it will no longer be able to provide acceptable levels of visibility.
Purchasers of high-visibility apparel should get proof that the materials used, and the design of the garment meet the requirements of the CSA Z96-15 Standard. Generally, the garment’s tag will state if it meets the requirements.
What are the different classes of safety apparel?
Back to topThe CSA Standard Z96-15, High-Visibility Safety Apparel sets out levels of retroreflective performance (i.e., the effectiveness of material in returning light to its source), the colours and luminosity of background materials, and how much of the body that should be covered by the high-visibility components. There are also special requirements for garments that also need to provide electrical flash and flame protection. Note that although specifications for apparel classes are similar to those in ANSI/ISEA 107, these CSA classes differ in that they specify body coverage rather than minimum areas.
CSA lists three classes of garments based on body coverage provided. Each class covers the torso (waist to neck) and limbs according to the minimum body coverage areas specified for each class.
- Class 1 provides the lowest recognized coverage and good visibility.
- Class 2 provides moderate body coverage and superior visibility.
- Class 3 provides the greatest body coverage and visibility under poor light conditions and at great distance.
Details for each of the classes are listed below. For more details on the exact specifications, please refer to the Standard. (Note: While the Standard does not set out the requirements for high-visibility apparel for specific jobs, it does provide some examples of jobs where the different classes may be appropriate.)
When would I wear the different classes of High-Visibility Safety Apparel?
Back to topLow Risk: Class 2, Class 1 under certain conditions
Low risk situations may include:
- Workers performing activities that permit their full and undivided attention to approaching traffic.
- When there is ample separation between workers on foot and traffic or other mobile equipment.
- When work backgrounds are not complex, allowing for optimal visibility.
- When vehicles do not exceed 40 km/h (25 mph).
- When workers are doing tasks that divert their attention from approaching traffic.
Examples of jobs include:
- Workers directing vehicle operators to parking or service locations.
- Workers retrieving shopping carts in parking areas.
- Workers in warehouse operations.
- "Right-of-Way" or sidewalk maintenance workers.
- Workers in shipping or receiving operations.
Figure 1
Example of Class 1 Apparel
Harness or Colour/Retroreflective Stripes on Other Clothing
NOTE: Other options are possible, including a shirt made of non-high-visibility material, but with high-visibility or retroreflective stripes/bands.
Medium Risk: Class 2 or 3 based on certain conditions
Medium risk situations may include:
- When vehicles or equipment are moving between 40-80 km/h (25-50 mph).
- Workers who require greater visibility under inclement weather conditions or low light.
- When work backgrounds are complex.
- When workers are performing tasks that divert attention from approaching vehicle traffic.
- When work activities are in closer proximity to vehicles (in or near flowing vehicle traffic).
Examples of jobs include:
- Roadway construction, utility, forestry or railway workers.
- Manufacturing, plant, or mill workers.
- Survey crews.
- School crossing guards.
- Parking and toll gate workers.
- Airport baggage handlers and ground crews.
- Emergency response personnel.
- Members of law enforcement.
- Accident site investigators.
- Railway workers.
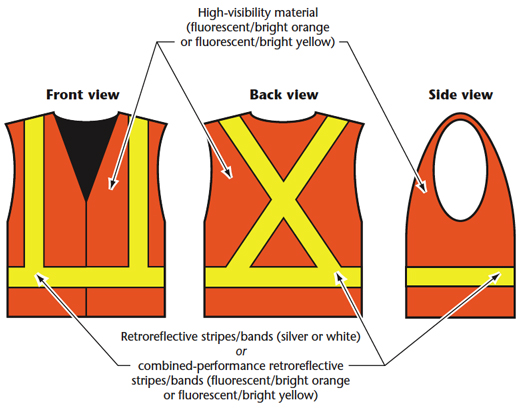
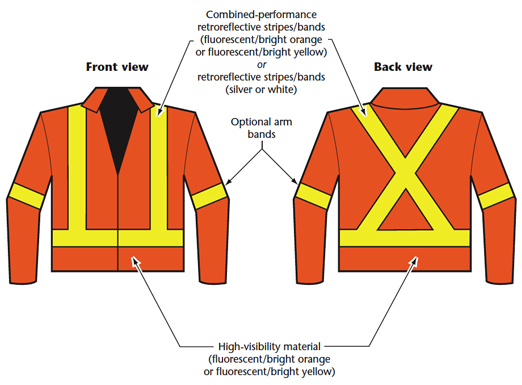
Figure 2
Examples of Class 2 Apparel
Vests, Jackets and Bib overalls
NOTE: These examples are not the only options available and are shown for example purposes.
High Risk: Class 2 for daytime, Class 3 for low-light conditions
High risk situations may include:
- Vehicle speeds exceeding 80 km/h (50 mph).
- Workers on foot and vehicle operators have high task loads that clearly place the worker in danger.
- When the wearer must be conspicuous through the full range of body motions at a minimum of 390 m (1,280 ft).
- Work activities taking place in low light or at nighttime.
Examples of jobs include:
- Roadway construction workers.
- Utility workers.
- Survey crews.
- Mine workers.
- Emergency responders.
- Road assistance or courtesy patrols.
- Flagging crews.
- Towing operators.
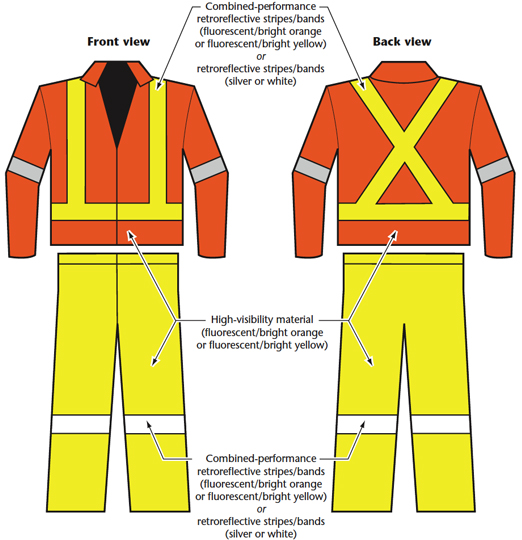
Figure 3
Examples of Class 3 Apparel
Jackets and Overalls
NOTE: These examples are not the only options available and are shown for example purposes.
From CSA Standard Z96-15.
What should worker training include?
Back to topAs with any personal protective equipment, workers must receive appropriate training in the use and care of the equipment. Workers wearing high-visibility apparel should know the following information:
- When to use the high-visibility apparel.
- Fitting instructions, including how to put on and take off the apparel, if relevant.
- The importance of using and wearing the apparel as intended.
- Limitations of use.
- How to store and maintain the apparel correctly.
- How to check for wear and tear.
- How to clean or decontaminate the apparel correctly, with complete washing or dry-cleaning instructions.
- Fact sheet last revised: 2021-12-17