WHMIS 1988 - Labelling Requirements
On this page
- What is a WHMIS label?
- Why label stuff?
- Who is responsible for labelling?
- Are there different types of labels?
- Is the content of supplier and workplace labels different?
- Do workplace labels have to have a hatched border?
- What happens if I put the material in a different container?
- What types of labels do I use if the material is shipped in bulk?
- Are workplace labels necessary if the material is in a pipe or reaction vessel?
- Are labels different if I work in a laboratory?
- What are the WHMIS symbols?
What is a WHMIS label?
Back to topIn Canada, the WHMIS (Workplace Hazardous Material Information System) label is one of the ways health hazard information is made available to anyone using the material. Labels are required by WHMIS laws.
Why label stuff?
Back to topLabels are important because they are the first alert there may be hazards associated with using the product covered by WHMIS legislation. The labels also tell what precautions to take when using the product. In addition, labels also inform the person that there is a Material Safety Data Sheet (MSDS) available which contains more detailed information on the product.
Who is responsible for labelling?
Back to topSuppliers are responsible for labelling WHMIS-controlled products that they provide to customers. Employers and sometimes employees are all responsible for labelling or relabelling products in the workplace, as directed in occupational health and safety legislation. This includes labelling controlled products with workplace labels, decanted products, laboratory chemicals or piping and bulk containers where a controlled product is being held or is flowing.
Are there different types of labels?
Back to topYes. A WHMIS label can be a mark, sign, stamp, sticker, seal , ticket, tag or wrapper. It can be attached, imprinted, stencilled or embossed on the controlled product or its container. However, there are two different types that are used most often: the supplier label and the workplace label.
Is the content of supplier and workplace labels different?
Back to topThere are slightly different requirements for what must be on the label depending on who is required to put the label on the product.
If a supplier label is not attached to a controlled product you are not to use the material until the supplier gives you an MSDS and a supplier label.
A supplier label must:
- appear on all controlled products received at workplaces in Canada
- contain the following information:
- product identifier (name of product)
- supplier identifier (name of company that sold it)
- a statement that an MSDS is available
- hazard symbols [the pictures of the classification(s)]
- risk phrases (words that describe the main hazards of the product)
- precautionary measures (how to work with the product safely), and
- first aid measures (what to do in an emergency)
- have all text in English and French
- have the WHMIS hatched border.
Supplier labels for materials from a laboratory supply house that are intended for use in a laboratory in amount less than 10 kg. and any controlled product sold in a container with less than 100 ml may contain less information than listed above.
If the product is always used in the container with the supplier label, no other label is required (unless the supplier label falls off or becomes unreadable). However, sometimes you will want to put some of the material into another container for use in the workplace. This new container does require a workplace WHMIS label.
A workplace label must:
- appear on all controlled products produced in a workplace or transferred to other containers by the employer
- may appear in placard form on controlled products received in bulk from a supplier
- have the following information:
- product identifier (product name)
- information for the safe handling of the product
- statement that the MSDS is available
- may contain the WHMIS hazard symbols or other pictograms.
These are the minimum requirements for workplace labels. The employer may wish to put more information on the labels but it is not required under the law.
Do workplace labels have to have a hatched border?
Back to topSupplier labels must have a hatched border around the information on the label but labels prepared in the workplace do not necessarily have to have hatched borders.
The Hazardous Products Act and the Controlled Products Regulations specify, among other things, what suppliers and importers are required to do with respect to MSDSs and labels. Section 20 of the Controlled Products Regulations prescribes label design requirements for supplier labels and Schedule III has a picture of how the label should look.
It is occupational health and safety legislation, not the Controlled Products Regulations, that describe what employer must do when preparing workplace labels. For example, section 10.41 on "Replacing Labels" in the Canada Occupational Safety and Health Regulations states:
"Where, in a work place, a label applied to a controlled product or a container of a controlled product becomes illegible or is removed from the controlled product or the container, the employer shall replace the label with a work place label that discloses the following information in respect of the controlled product
(a) the product identifier;
(b) the hazard information; and
(c) a statement indicating that a material safety data sheet is available in the work place."
This section does not require employers to use WHMIS symbols and a hatched border when preparing workplace labels. However, nothing in the regulations prevents an employer from using the WHMIS requirements for designing supplier labels when prepare workplace labels. Provincial OH&S legislation have similar provisions.
What happens if I put the material in a different container?
Back to topYou must use a workplace label on the container. There are two special cases when a workplace label is not necessary. When a controlled material is poured into a container and it is going to be used immediately, no label is required. Also, if the material is "under the control of the person who decanted it" (which means if the person who poured it will be the only one using it) and if the material is all used during one shift, just the product identifier (name) is required. However, if the material is not used right away or if more than one person will be in control of the material, a workplace label is required. Your company may have special rules about labelling containers so you should ask about labelling policies.
What types of labels do I use if the material is shipped in bulk?
Back to topMaterial that is shipped in bulk also follows special rules. The tank or container that the bulk material is transferred into must be labelled with either a supplier label or a workplace label. When the material is moved into containers for resale or delivery out of your workplace, you must put a supplier label on each container. When the bulk material is used in your workplace (usually transferred into smaller containers), a workplace label is required on the containers.
Are workplace labels necessary if the material is in a pipe or reaction vessel?
Back to topNot necessarily. Pipes and reaction vessels may be marked in other ways such a colour coding, or placards. However, it is the employers duty to train workers how to recognize and interpret the markings used in your workplace.
Are labels different if I work in a laboratory?
Back to topSometimes. Laboratory samples of controlled products that are less than 10 kilograms do not have to have a WHMIS label as long as there is a label which states the following in both English and French:
- the product identifier (name)
- the chemical identity or generic chemical identity of an ingredient of the controlled product, if known
- the supplier identification
- the statement "Hazardous Laboratory Sample. For hazard information or in an emergency, call..." and an emergency telephone number must be provided
What are the WHMIS symbols?
Back to topClass A - Compressed Gas
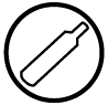
- Contents under high pressure.
- Cylinder may explode or burst when heated, dropped or damaged.
Class B - Flammable and Combustible Material
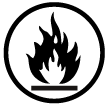
- May catch fire when exposed to heat, spark or flame.
- May burst into flames.
Class C - Oxidizing Material
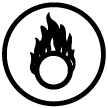
- May cause fire or explosion when in contact with wood, fuels or other combustible material.
Class D, Division 1 - Poisonous and Infectious Material: Immediate and serious toxic effects
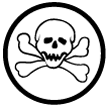
- Poisonous substance.
- A single exposure may be fatal or cause serious or permanent damage to health.
Class D, Division 2 - Poisonous and Infectious Material: Other toxic effects
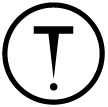
- Poisonous substance.
- May cause irritation.
- Repeated exposure may cause cancer, birth defects, or other permanent damage.
Class D, Division 3 - Poisonous and Infectious Material: Biohazardous infectious materials
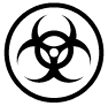
- May cause disease or serious illness.
- Drastic exposures may result in death.
Class E - Corrosive Material
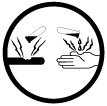
- Can cause burns to eyes, skin or respiratory system.
Class F - Dangerously Reactive Material
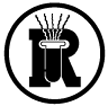
- May react violently causing explosion, fire or release of toxic gases, when exposed to light, heat, vibration or extreme temperatures.
- Fact sheet confirmed current: 2009-06-25
- Fact sheet last revised: 2001-07-25